Revision of Plinth area Norms for GPRA to be constructed for Central Govt. Employees w.e.f. 2024: MoHUA
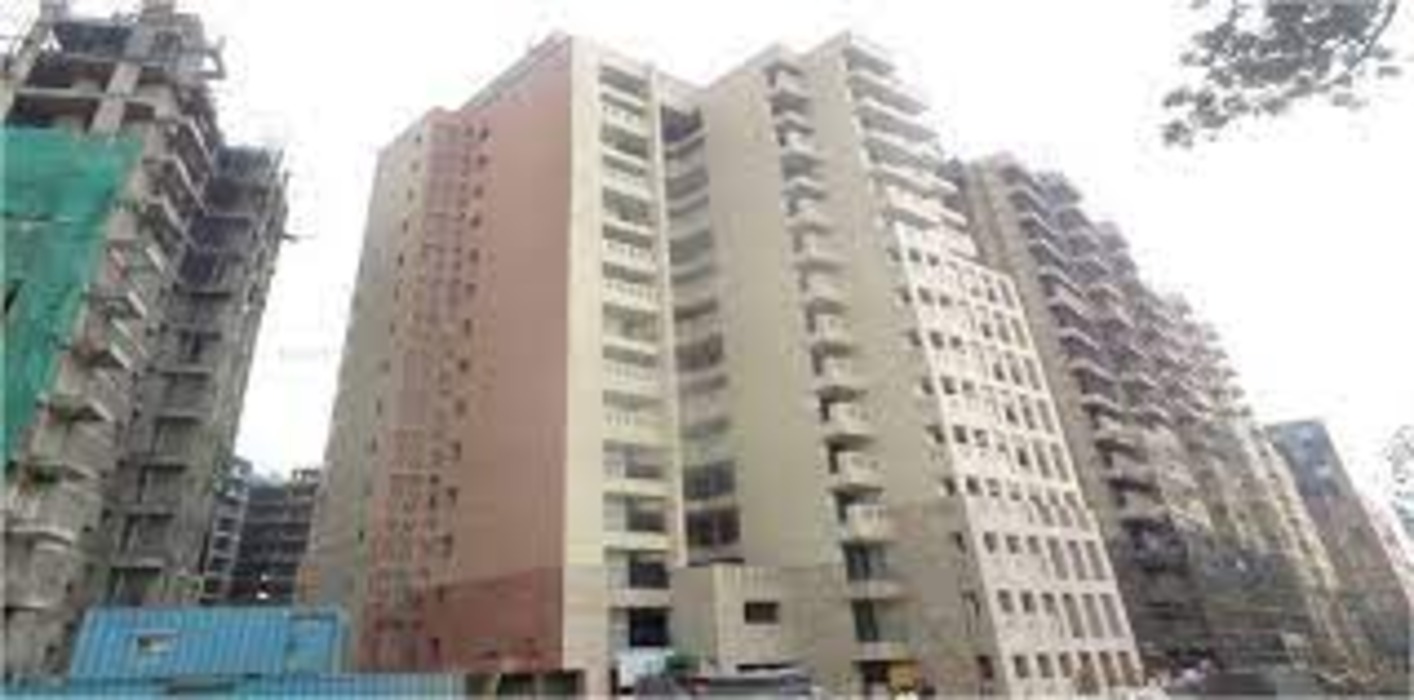
Revision of Plinth area Norms for GPRA to be constructed for Central Govt. Employees and its applicability to Central Govt. Departments w.e.f. 2024: MoHUA Corrigendum dated 23.02.2024
F. No. 28012/08/2023-WI
Government of India
Ministry of Housing and Urban Affairs
Works Division
****
Nirman Bhawan, New Delhi.
Dated 23.02.2024.
CORRIGENDUM
Sub: Revision of Plinth area Norms for General Pool Residential Accommodation (GPRA) to be constructed for Central Govt. Employees and its applicability to Central Govt. Departments-regarding
In partial modification to the Department’s O. M. of even no. dated 23.01.2024 vide which revision of Plinth Area Norms for General Pool Residential Accommodation (GPRA) to be constructed for Central government Employees and its applicability to Central Govt. Departments was issued, and to convey that bedrooms for type-II and type-III, as indicated in the annexure -2 of the table (in column Bedrooms) in the said O.M. may be read as:
Category | Bedroom | Bedroom | |
Read as | Instead of | ||
Type -II | Two | Two plus study | |
Type -III | Two plus study | Two |
2. The other terms and conditions of the O.M. dated 23.01.2024 will remain the same.
3. This issues with the approval of the competent authority.
(Gajendra W. Bhelawe)
Under Secretary to the Govt. of India
Ph: 23060639
No. 28012/08/2023-WI
Government of India
Ministry of Housing & Urban Affairs
(Works Division)
Nirman Bhawan, New Delhi
Dated : 23rd January, 2024
OFFICE MEMORANDUM
Subject: Revision of Plinth Area Norms for General Pool Residential Accommodation (GPRA) to be constructed for Central Govt. Employees and its applicability to Central Govt. Departments-regarding
Ministry of Housing and Urban Affairs (MoHUA) being the nodal ministry for providing houses under General Pool Residential Accommodation (GPRA) for Central Government Employees all over India, was undergoing the process of revision of Plinth Area Norms applicable to GPRA Colonies. These norms are also used by various Government Departments and PSUs for their Departmental Housing like Income Tax, Central Excise ete.
2. The norms for GPRA presently applicable were last notified 10 years back by the Ministry vide OM No.-2201 1/01/2008-W3 dated 07.08.2013. The plinth Area Norms issued in 2013 included fixing area and size of dwelling units along with eligibility as per pay scales, general design guidelines, scale of amenities and general specifications. The design/plan of the residential quarters to be constructed were to be developed based on specific site condition, requirements of climate and region etc. The local building Bye Laws like that of parking were also required to be followed during planning.
3. The Plinth Area Norms were notified for the first time in 1962 and since then MoUD/MoHUA has been regulating these provisions. The experience gained during the past 10 years during which construction of new colonies and redevelopment of seven GPRA colonies have been taken up by CPWD and NBCC. The decade gone by has also witnessed sustained growth in economic prosperity on account of increase in income after implementation of the 7th Pay Commission. As a result, the household items and goods of general utility like washing machine, microwaves, air-conditioners etc. are now uniformly available right from the Type-2 house occupants to the Type 6 & 7 occupants.
4. The above scenario has resulted in increased need of storage spaces for various purposes like IT equipment, large wardrobes, increased area in kitchen, utility balconies, living room balconies etc. The fact that such spaces and specification are finding high usage as well as selling focus point in real estate projects being taken up by private sector now, thus brining direct comparison. This is extremely relevant in case of Type II, IJ and IV GPRA quarters, which were on the smaller side till now and specification affected by view towards economy. Thus, the norms for category Type II, III] & IV houses are not in tune with the present day living standards holds true.
5. After detailed deliberations on revision of plinth area norms, it 1s decided to revise the Plinth area norms of residential quarters under GPRA Colonies for Central Government Employees as under :
Plinth Area Norms for GPRA
(in Sq. mtr.)
Type | 2013 | 2024 | |
I (A) | Main Unit | 49.5 | No new construction |
II (B) | Main Unit | 63.00 | 75.00 |
III (C) | Main Unit | 73.00 | 85.00 |
IV (D) | Main Unit | 101.50 | 110.00 |
Servant Unit | 19.50 | 25.00 | |
V (E) | Main Unit | 161.50 | 161.50 |
Servant Unit | 25.00 | 25.00 | |
VI (F) | Main Unit | 229.00 | 229.00 |
Servant Unit | 25.00 | 25.00 | |
VII (G) | Main Unit | 331.00 | 331.00 |
Servant Unit | 23.5*2 | 25*2 | |
VIII (H) | Main Unit | 460.00 | 460.00 |
Servant Unit | 23.5*4 | 25*4 |
6. Scale of amenities
a. General Design Guidelines at Annexure-1.
b. Scale of amenities at Annexure-2.
c. Scale of civil fittings and fixtures at Annexure-3.
d. Scale of amenities for electrical fittings and fixtures at Annexure-4.
7. General specifications
General specifications of flooring, doors, windows, water supply, sanitary installation and other services are given in Annexure-5.
8. Parking Norms
The parking norms of the local body shall be followed.
This issues with the approval of the Secretary (HUA).
Enclosure: Annexure 1 to 5
(Amrendra Kumar Sinha)
Under Secretary to the Govt. of India
Annexure-I
General Design Guidelines
Guidelines given below may be adopted while designing GPRA houses.
- Minimum floor to floor height may be kept as 3,000 mm.
- Generally, no room or space of less than 1,800 mm may be designed.
- The size of toilets may be minimum 1,500 mm x 2,100 mm, but it is desirable to design bigger toilets. All water closets must have a wash basin also.
- Generally, duplex units may be avoided. However, if designed, provision of pantry of adequate size may be made at the first-floor level.
- Utility balcony may be avoided on front side of the building. Utility Balcony to be provided in all unit types.
- Balcony must be provided in all the climatic regions of the country. These balconies may be enclosed with glaze windows only in the hilly regions. The area of balconies may vary with the design depending on the architectural & structure considerations. Minimum depth 1,200 mm
- Windows may be designed for window type ACs in all bedrooms, living and drawing rooms. Provision for power points and drainage of split/window type ACs may also be made.
- The layout of electrical points, fittings and fans shall match with furniture layout. The staircase and balcony railing may be made of SS 316 or cast iron or timber. Large size granite stone slabs may be used in common circulation areas.
- Community facilities like community hall, milk booth, vegetable shop, grocery store, dry-cleaning shop etc. may be provided, if required.
- The main entrance to the building may be designed for barrier free access. As far as possible, stilt may be avoided.
- Wherever required, additional area for staircase, circulation, porch and services like electrical sub-station, pump house, meter room, guard room etc. will be allowed over and above the norms. Staircase and circulation to be as per local bye laws/NBC.
- Shafts for services like water supply, drainage and sanitary pipes, electrical and communication lines will be allowed over and above the norms.
- Generally, no deviation from the prescribed norms should be made, but if any deviation becomes essential, proposal for such deviation should be referred to for specific approval of the owner organization on case-to-case basis.
- The proposed plinth area Norms are based on standard single brick wall of 230 mm (9”) and shall be applicable to modular masonry of size 200 mm (8”). However where the wall thickness has to be increased for technical reasons like cavity-wall for green building construction or for use of local material like stone etc. the plinth area may be suitably increased.
Annexure-2.
Plinth Area Norms for General Pool Residential Accommodation (GPRA) for Central Government employees
Scale of Amenities:
S No | Category | Office | Drawing Room | Dining Room | Bed Rooms | Kitchen | Store | Number of Attendant’s Unit | Utility Balcony | Toilets |
1 | Type–II | — | One | — | Two | One | — | — | One | Two |
2 | Type-III | — | One | — | Two plus study | One | — | — | One | Two |
3 | Type-IV | — | One | One | Three | One | – | One | One | Three |
4 | Type-V | — | One | One | Three | One | One | One | Two | Three |
5 | Type-VI | — | One | One | Four | One | One | One | Two | Three |
6 | Type-VII | One | One | One | Four | One | One | Two | Two | Four* |
7 | Type-VIII | One | One | One | Four | One | One | Two | Two | Four* |
8 | Attendant’s unit | — | — | — | One | One | — | — | One | One |
*One toilet (without bath) shall be provided attached with office.
Annexure-3
Plinth Area Norms for General Pool Residential Accommodation (GPRA) for Central Government employees
Scale of Civil Fittings and Fixtures
S No | Item | Type-II & II | Type-IV | Type V & VI | Type-VII & VIII | Attendant Unit | |||||
1 | Kitchen | Old | New | Old | New | Old | New | Old | New | Old | New |
(i) | Granite cooking platform | Yes | Yes | Yes | Yes | — | Yes | — | Yes | Yes | Yes |
(ii) | Stainless steel 316 kitchen sink with drain board | Yes 034 grade | Yes | Yes | Yes | — | Yes | — | Yes | Yes | Yes |
(iii) | Modular cupboard with shelves and drawers | — | Yes | — | Yes | Yes | Yes | Yes | Yes | — | Yes |
2 | Built in wardrobe in each bedroom up to ceiling height, minimum about 900 mm wide and 600 mm deep. It may be made up of 18 mm thick blackboard or wood composite plastic or steel. The inner side of one shutter may have mirror of size 600 mm x 1200 mm approx. | Yes | Yes | Yes | Yes | Factory made wardrobe | Yes | Factory made wardrobe | Yes | Yes | Yes |
3 | Magic eye in front entry door | Yes | Yes | Yes | Yes | Yes | Yes | Yes | Yes | Yes | Yes |
4 | Curtain rod with required accessories, except for kitchen and toilet doors and windows
= |
Yes | Yes | Yes | Yes | Yes | Yes | Yes | Yes | Yes | Yes |
5 | 18 mm thick granite window sill lining | Yes | Yes | Yes | Yes | Yes | Yes | Yes | Yes | Yes | Yes |
6 | Indian or European or wall hung WC pan with flushing cistern | Yes | Yes | Yes | Yes | Yes | Yes | Yes | Yes | Yes | Yes |
7 | Water jet spray/ Hand faucet with each IWC/EWC | Yes | Yes | Yes | Yes | Yes | Yes | Yes | Yes | No | Yes |
8 | Wash basin with CP brass mixer tap in each toilet | Yes | Yes | Yes | Yes | Yes | Yes | Yes | Yes | Yes | Yes |
9 | Wash basin in balcony. Tap for washing machine | No | Yes | No | Yes | No | Yes | No | Yes | No | No |
10 | Taps in kitchen, toilets and balcony, director supply connection in kitchen | Yes
Not in balcony |
Yes | Yes
Not in balcony |
Yes | Yes
Not in balcony |
Yes | Yes
Not in balcony |
Yes | Yes
Not in balcony |
Yes |
11 | Swan neck CP brass mixer tap in kitchen sink | No | Yes | No | Yes | No | Yes | No | Yes | No | Yes |
12 | Shower with CP brass mixer tap | Yes | Yes | Yes | Yes | Yes | Yes | Yes | Yes | Yes | |
13 | SS 316 towel rail | Yes
CP Brass |
Yes | Yes
CP Brass |
Yes | Yes
CP Brass |
Yes | Yes
CP Brass |
Yes | Yes
CP Brass |
Yes |
14 | SS 316 toilet paper holder | Yes
CP Brass |
Yes | Yes
CP Brass |
Yes | Yes
CP Brass |
Yes | Yes
CP Brass |
Yes | No | Yes |
15 | Mirror of size 450 x 600 mm or of bigger size | Yes | Yes | Yes | Yes | Yes | Yes | Yes | Yes | Yes | Yes |
16 | Granite quadrant of 250 mm radius near shower, one at 1200 mm and second at 1500 mm height | No | Yes | No | Yes | No | Yes | No | Yes | No | Yes |
17 | Plumbing for water filter and geyser | Yes | Yes | Yes | Yes | Yes | Yes | Yes | Yes | Yes | Yes |
18 | Terrace water tank of 500 litres capacity | Yes | Yes | Yes | Yes | Yes | Yes | Yes | Yes | Yes | Yes |
19 | Facility for IGL pipeline, where applicable | No | Yes | No | Yes | No | Yes | No | Yes | No | Yes |
20 | PVC pipe for drainage of water from ACs | No | Yes | No | Yes | No | Yes | No | Yes | No | No |
21 | Provision for window A/Cs in each room | No | Yes | No | Yes | No | Yes | No | Yes | No | No |
22 | Provision for split A/Cs in each room | No | Yes | No | Yes | No | Yes | No | Yes | No | No |
Annexure-4:
Plinth Area Norms for General Pool Residential Accommodation (GPRA) for Central Government employees
Scale of Electrical Fittings and Fixtures
S No | Item | Type-II & II | Type-IV | Type V & VI | Type-VII & VIII | Attendant Unit |
1 | Light fittings, minimum one in each room and kitchen | Yes | Yes | Yes | Yes | Yes |
2 | Bracket or decorative lights, minimum one in each room balcony, each toilet and mirror light for each bathroom | Yes | Yes | Yes | Yes | Yes |
3 | Fans(minimum one decorative in each room) | Yes | Yes | Yes | Yes | Yes |
4 | Modular switches | Yes | Yes | Yes | Yes | Yes |
5 | 5 A sockets (minimum two in each room and kitchen) | Yes | Yes | Yes | Yes | Yes |
6 | 15 A sockets (minimum two in each room and kitchen) | Yes | Yes | Yes | Yes | Yes |
7 | A socket with MCB for geyser in each toilet and kitchen | Yes | Yes | Yes | Yes | Yes |
8 | 15 A socket with MCB for AC in each room | Yes | Yes | Yes | Yes | — |
9 | 5 A and 15 A sockets, one each, in balcony , and utility area , store | Yes | Yes | Yes | Yes | Yes |
10 | Call bell near main door | Yes | Yes | Yes | Yes | Yes |
11 | Electric chimney in kitchen | — | — | Yes | Yes | — |
12 | Fresh air exhaust fan in kitchen and each toilet | Yes | Yes | Yes | Yes | Yes |
13 | 25 liters geyser in each toilet | Yes | Yes | Yes | Yes | — |
14 | Telephone and cable TV sockets & modular mobile charging socket each room | Yes | Yes | Yes | Yes | Yes |
15 | Electrical points for water filter and oven | Yes | Yes | Yes | Yes | Yes |
16 | Electrical point for fridge and washing machine | Yes | Yes | Yes | Yes | Yes |
17 | Call bell point with image display system | Yes | Yes | |||
18 | Dressing light point | Yes | Yes | Yes | Yes | Yes |
Annexure 5
General Specifications and Design for GPRA Dwelling Units
The materials, specifications and design values given here are only illustrative. Use of local and renewable materials shall be preferred. The actual design values may vary according to type of building, bye-laws, and special requirements, if any.
Sl. No. | Description | Specifications and design |
Civil |
||
1 | Foundation | |
i | Bearing capacityqa | 60 kN/m2 at 2500 mm below the ground level |
ii | Ground water table | 7 meter below ground during rainy season |
iii | Type | Bored cast in situ RCC piles of M30 concrete with minimum cement content of 350 kg/m3 |
iv | Masonry | Fly ash cement concrete bricks in cement mortar 1:6 |
2(a) | Superstructure | RCC framed structure |
i | Concrete mix | M 30 |
ii | Rebars | Corrosion resistant Fe 550 D |
iii | External walls | 230 mm thick fly ash cement concrete brick masonry with cement mortar 1:6. OR 200 mm thick autoclaved aerated concrete blocks laid with adhesive. |
iv | Internal Walls | 115 mm thick fly ash cement concrete brick masonary with cement mortar 1:4. OR 100 mm thick autoclaved aerated concrete blocks laid with adhesive. |
2b | Superstructure | Load bearing masonry in burnt clay FPS bricks. |
i | Load bearing walls | 230 mm thick brick masonry in cement mortar 1:6. |
ii | Partition walls | 115 mm thick brick masonry in cement mortar 1:4. |
3 | Doors | |
i | Entrance Door | 2nd class teak wood frame and 2- leaf shutters. 35 mm thick decorative flush door shutter. The frames will have double rebate for wire mesh shutters. |
ii | Room frames | 2nd class teak wood or UPVC. |
iii | Room Shutters | 35 mm thick decorative or commercial flush door. |
iv | External doors | 35 mm thick flush door shutters or UPVC. Exposed face of shutters in balcony or mumty will be protected with 1 mm thick PVC rigid foam sheet fixed using rubber based adhesive. |
v | Toilets | Frames and 25 mm thick shutters made of wood fibre composite board of density 650 kg/m3. |
vi | Wire gauze shutters (for all external doors) | Wire mesh of SS 304 stainless steel. |
vii | Architraves | Teak wood or wood fibre composite or UPVC. |
4 | Windows | |
i | Frames | 2nd class teak wood or UPVC extruded profiles having
2.3 mm thick wall. |
ii | Shutters | 2nd class teak wood or UPVC extruded profiles having
2.3 mm thick wall. |
iii | Fixed glazing | 2nd class teak wood or UPVC extruded profiles having
2.3 mm thick wall. |
iv | Toilets | 5mm glass louvers in colour anodized aluminium frame |
v | Wire gauze shutters (for all external) | Wire mesh of SS 304 stainless steel. |
vi | Window sill level | Rooms: 900 mm, Toilets: 1225 mm, Kitchen: 1225 mm |
5 | Wardrobes | Boxes and shelves of 19 mm thick commercial block board, shutters of 19 mm teak veneered or laminated or commercial block board. OR boxes, shelves and shutters of 18 mm thick wood fibre composite board of density 650 kg/m3 .20 mm diameter aluminium hanger rods with slotted (non screw type) brackets. Clear distance of hanger rod below the board bottom: 40 mm . Or S.S 304 |
6 | Kitchen cupboards | Boxes shelves, and shutters of teak veneered or commercial or laminated 19 mm thick block board OR 18 mm thick wood fibre composite board of density 650 kg/m3. Stainless steel drawers with telescopic channel. |
7 | Hardware fittings | ss 304 stainless steel. OR colour anodized aluminum 125
*64*1.90 mm stainless steel butt hinges |
8 | Curtain rods | Elliptical shaped SS 304 stainless steel with heavy duty non-screw type brackets and finials. Height 100 mm above window top. |
9 | Flooring and skirting | |
i | Circulation areas | 18 mm thick gang saw cut granite of light shade with contrast border. The skirting will not project beyond wall surface. Staircase skirting will be parallel to waist slab. |
ii | Rooms | 18 mm thick gang saw cut granite of light shade. |
iii | Kitchen | Satin matt vitrified tiles of minimum size 600*600 mm. |
iv | Kitchen platform | 18 mm thick gang saw cut black granite; edges rounded. Height above finished floor level: 900 mm Granite slab will be supported over19 mm thick block board boxes, no RCC slab is required for modular kitchen platform. |
v | Kitchen dado | Above platform: 600 mm high with vitrified tiles of size 600*600 mm OR with ceramic tiles of size 600*300 mm. Elsewhere: full height dado of same tiles. |
vi | Toilets and WC | Anti-skid ceramic tiles of size 300*300 mm. Two granite corners of 250 mm radius will be fixed in wall near shower, first at 1200 and second at 1500 mm height. |
vii | Toilet dado | Vitrified tiles of size 600*600 mm OR ceramic tiles of size 600*300 mm up to ceiling. One decorative band. |
viii | Wash basin counter | Counter and 100 mm high skirting with 18 mm thick gang saw cut black granite. Edges rounded. 1500 mm high dado of vitrified tiles of size 600*600 mm OR 1500 mm dado of ceramic tiles of size 600*300 mm. Only under countertop wash basins will be used. |
ix | Window sill | 18 mm thick gang saw cut black granite, edges rounded, and projecting 12mm from finished wall surfaces. |
10 | Parapet walls | 1200 mm high, 230 mm thick. Top finished with black granite, sloping inwards edges rounded, projecting 12mm from finished wall surfaces. |
11 | Balustrade/railing | 1200 mm high powder coated aluminium sections or factory made SS 304 stainless steel. OR cast iron. |
12 | Terracing | Vitrified tile of size 600*600 mm with adhesive or crazy marble flooring. The RCC roof slab will be cast with a slope of 1:100. |
13 | Sanitary fittings | CP brass fittings Sanitaryware of reputed brands. Rigid PVC or GI waste pipe for wash basins and kitchen sinks. |
14 | Sanitary ware height | Wash basin top: 800 mm Urinal lip top: 600 mm Shower: 2100 mm
Mirror: 1200 mm Towel rail: 1500 mm WC faucet: 300 mm |
15 | Internal services | |
i | Rain water pipes | 150 mm diameter UPVC pipes clamped over MS heavy duty brackets 50 mm away from wall surface. |
ii | Soil and waste pipes | 100 mm diameter centrifugally cast (spun) iron pipes and fittings. OR UPVC pipes and fittings. All pipes shall be 50 mm away from wall surface, clamped over MS heavy duty brackets. No pipe will be < 75 mm diameter. |
iii | Floor traps | Long arm P-type floor traps placed at a corner of toilet Each floor trap outlet will be separate and join the vertical stack
externally. No Nahani traps shall be used. |
iv | Spouts | 75 mm diameter UPVC OR GI spouts, projecting 150 mm beyond wall surface, sloping outwards, laid 5 mm below floor level. End of pipe shall be cut at 45°. |
v | Sewer lines | HOPE pipes. Cushion of 600 mm. |
vi | Manholes | At 30 metre centres, and at bends and junctions. |
vii | Terrace tanks | 4 PVC tanks of 1000 litres capacity each, with screw type lid. Tanks will be placed over 1200 mm wide RCC slab cantilevering from a beam spanning over two columns. The top of slab will be 900 mm above the terrace level. OR SS |
16 | Finishing | |
i | Cement plaster | 1:6 mortar with well graded coarse sand. |
ii | Internal walls, ceiling | Low VOC acrylic paint over cement-based putty. |
iii | External walls | Low VOC textured or smooth acrylic paint over cement based putty. |
iv | Wood and steel | Synthetic enamel paint. |
v | Brick-RCC junction | 200 mm wide polypropylene wire mesh with U-clip will be used at the junction before plastering. |
17 | Modular Kitchen | The cabinets will be made of 18 mm thick wood fibre composite board of density 650 kg/m3 OR galvanized steel.
No RCC slab Is required for kitchen platform. |
18 | Clothes lines | Three or four rows of PVC coated steel wire 450 mm apart, tied to 75 mm long J hooks fixed with m-seal. |
Electrical | ||
1 | Wiring | FRLS PVC insulated single core copper wiring of 1.5 mm2 for light and 4 mm2 for power points. Concealed wiring in recessed medium class PVC conduits. Separate conduits from mains for wiring of essential, non-essential, and UPS distribution system. |
2 | Electrical fittings | Modular switches and sockets. Energy efficient LED luminaries of minimum 110 lumen per watt. 5-star, brushless direct current motor fans of 1200 mm sweep. Occupancy sensors. Master switch outside hostel and guest house rooms. Fittings will be provided as per furniture lay out.
Minimum two 5A and one 15A sockets will be provided in each room. Fans and light shall be fitted symmetrically as per furniture lay out Height of fittings: Switch board centre: 1200 mm Tube light or lamps: 2400 mm, 16A sockets: 300 mm |
3 | Exhaust fans | 125 mm inline duct booster exhaust ventilation fan |
4 | Escape lighting | Escape routes to get illuminated from an independent power source within 5 sec of power failure. The luminaries shall be mounted at 2400 mm height. |
5 | Exit signage | Green colour photo luminescent exit signs of size 450*150 mm at 2400 mm height at 30 m intervals and at all changes in direction. |
6 | Distribution Boards | Powder coated, prewired DBs with detachable cassette for safe removal of MCBs, RCCBs and terminal blocks. |
7 | Phone and TV cables | Only on specific requirement, telephone and coaxial TV cables will be provided in recessed PVC conduits |
8 | LAN | Core switches, L2 switches, gigabit switch, SFP modules, OFC, wi-fi access and controller. |
9 | Uninterruptible power systems | Online (double conversion voltage and frequency independent) UPS shall comply with IEC 62040-3 to provide continuous power to life safety circuits and sensitive equipment. It must have both static bypass switch and manually operated bypass switch for maintenance. Battery banks shall be designed to provide at least 30 minutes back- up at full load. |
10 | Lifts | Two regenerative lifts of 20 persons capacity each, with speed of 1.5 mis, microprocessor-based control, and variable voltage variable frequency drive system for AC motor. It should be equipped with automatic rescue device and maintenance free dry batteries, It should meet accessibility requirements for especially abled persons. like minimum lift size of 1500 mm x 1500 mm, minimum door width of 900 mm, call button, control panel, hand rails, and audio and visual indicators |
11 | Air-conditioning | Two modular air cooled variable refrigerant flow outdoor units of 20 HP capacity each with inverter type scroll compressor and R410 A refrigerant, suitable to deliver coefficient of performance (CoP) of minimum 4.7 at 50% load. High wall type indoor units of 2 TR capacity each. |
12 | Fire alarm system | The intelligent addressable fire alarm system (AFAS) will integrate public address, lifts, fire fighting, pressurization and smoke management systems. |
13 | Fire fighting system | The wet riser system will consist of electric pump, diesel pump, jockey pump, all suitable for automatic operation and control panel for pumps in a pump room near the underground sump, delivery pipe, terrace pump and air vessel. Powder coated MS glazed cabinet will be provided for wet riser shaft on each floor to encase one 150 mm diameter C class MS delivery pipe, fire hose box containing two reinforced rubber lined hose pipes each of 63 mm diameter and 15 m length with 20 mm diameter nozzle, powder coated MS hose reel disc with 30 m long rubber braided hose of 20 mm nominal diameter and 19 m shut off nozzle and hydrant landing valve. Four-way and three-way fire brigade inlet connection valves will also be provided in the sump and riser respectively. The landing valve, hose coupling, fire brigade inlet connection valve etc, will be of stainless steel. The yard hydrant will consist of ring main of 200 mm diameter C class MS pipe, hydrants spaced at 45 metre centres and connected to ring main with 80 mm diameter MS pipe, and fire hose box containing two reinforced rubber lined hose pipes each of 63 mm diameter and 15 m length with 20 mm diameter nozzle. The clear size of wet riser shaft will be 1200*800 mm. |
14 | Ventilation system | The basement and corridors will have supply air fans, ducts, grills, and exhaust air fans. The lift shaft, lift lobby and staircase will have pressurization system consisting of axial flow fan. Fan motor and casing shall be suitable for smoke exhaust application having thermal rating of 250o C for 2 hours as per BS EN12101-3: 2015. The ventilation system will be designed for minimum 12 air change per hour and pressure differential of 25 to 30 Pa. |
15 | Lightning protection | Single prong finial with GI tape of 20 mm*3 mm suitably earthed lo the ground. |
Bulk services |
||
1 | Compound wall | Low height compound wall is preferable. The maximum height may be 2100 mm, with 1500 mm high masonry and 600 mm high MS grill. The length of each wall panel may be 3600 mm centres. Expansion joint will be provided at 45 metre centres. The entrance gate, wall panels, coping, and grill will be designed aesthetically. About 1200 mm wide strip along the wall will be used for plantation. laying cables and pipes. |
2 | Buildings in hills | Hill slopes of up to 30o are generally stable. Therefore, building sites will be located on hillside with slope is 45o, preferably on south slope for more heat gain. Stepped terrace development and stepped storey construction will be adopted for economy and environment protection. |
3 | Levelling | The entire plot will be levelled to a slope of 300:1 to allow natural drainage of rain water. |
4 | Internal roads | 6 meter wide carriage way with 2% camber. 750 mm wide unpaved shoulders on both sides sloping outwards to drain off rain water. Paver finished bituminous road section will consist of 150 mm GSB, 150 mm WMM 50 mm BM and 40 mm thick bituminous concrete OR 150 mm thick vacuum dewatered M 30 concrete laid over 100 mm thick base of M10 concrete, in chequered bays of maximum 3*3 metre size. The grooves will be 5 mm wide, 50 mm deep and filled with suitable sealant |
5 | Footpath | 200 mm high and 1200 mm wide footpath finished with 60 mm thick paver blocks of M30 and kerb stone |
6 | Tube Well | One 200 mm diameter, 100 m deep tube well with uPVC pipe. Distribution network of CPVC pipes |
7 | Underground Sump | |
RCC sump of 200 kl capacity, with 10 HP submersible pump. The floor and walls will be finished with vitrified tiles of size 600*600 mm. The first compartment of 100 kl will be used for firefighting. | ||
8 | Filtered water supply | Tube well water will be chlorinated and fed into the UG sump. Water from the sump will be pumped to terrace tanks through CPVC distribution lines. |
9 | Sewerage system | HOPE pipes of 300, 200, and 100 mm diameter laid to minimum slope of 300:1. Manholes at 30 m intervals. 100 kl sewage treatment plant on MBBR technology |
10 | Recycled water | Treated water from STP will be collected into a sump and pumped for horticulture purpose through CPVC distribution lines. The hydrants will be of ball cock type. |
11 | Rainwater harvesting | 2 pits each of size 1.5*2*2 m with borewell of 100 mm diameter and 15 m depth |
12 | Sub-station | Two 1250 kVA, 5-star, 3 phase dry type 11 kV/433-250 V transformers, HT panel, LT panels, APFC panel, and surge protection device. |
13 | DG set | Two 250 kVA 3 phase DG set with AMF panel mounted on platform of size 7000*6000 mm. Shed of MS tubular truss and galvalume sheet. |
14 | Solar power | On grid, roof top solar PV plant of 250 kWp installed capacity with monocrystalline cell panels of minimum 20% efficiency. Power conditioning unit. Net metering and data monitoring system. |
15 | Street lights | LED fitting over 9 m high ornamental MS/CI poles |
16 | Horticulture works | Grassing in select areas, tree and shrub plantation |
General |
||
1 | Floor height (minimum) | Residential: 3000 mmNon-residential: 3300 mm 3600 mm with sprinklers. False ceiling height 2700 m |
2 | Pantry | Pantry of minimum 1800 width may be provided on each floor of a non-residential building. It may have 600 mm wide platform and one kitchen sink |
3 | Toilets | Each water closet will be provided with a wash basin. Wherever feasible, sanitary ware will be provided on external wall of the building. The clear depth of sunken slab for Indian WC will be 600 mm and that for EWC will be 300 mm to accommodate pipes, traps, and slope |
4 | Accessible terrace | All the buildings with flat roof will have accessible terrace for ease of maintenance. |
5 | Retaining walls | Generally, the hill slope will not be cut steeper than 60o from the horizontal for its stability. Where unavoidable, retaining wall will be provided with weep holes of 100 mm diameter PVC pipes at 1500 mm centres in staggered manner embedded at 10o downward slope, projecting by 150 mm beyond the wall on the valley side. Inverted filter will be provided behind the wall. About 300 mm thick silty clay layer of back-fill with grass will be provided flush with the top of retaining wall to prevent seepage of water in the back-fill. The back-fill itself will be of self-draining soil like coarse sand or gravel, free of fines. Grass turfing on toe side to prevent toe erosion |
Source: MOHUA